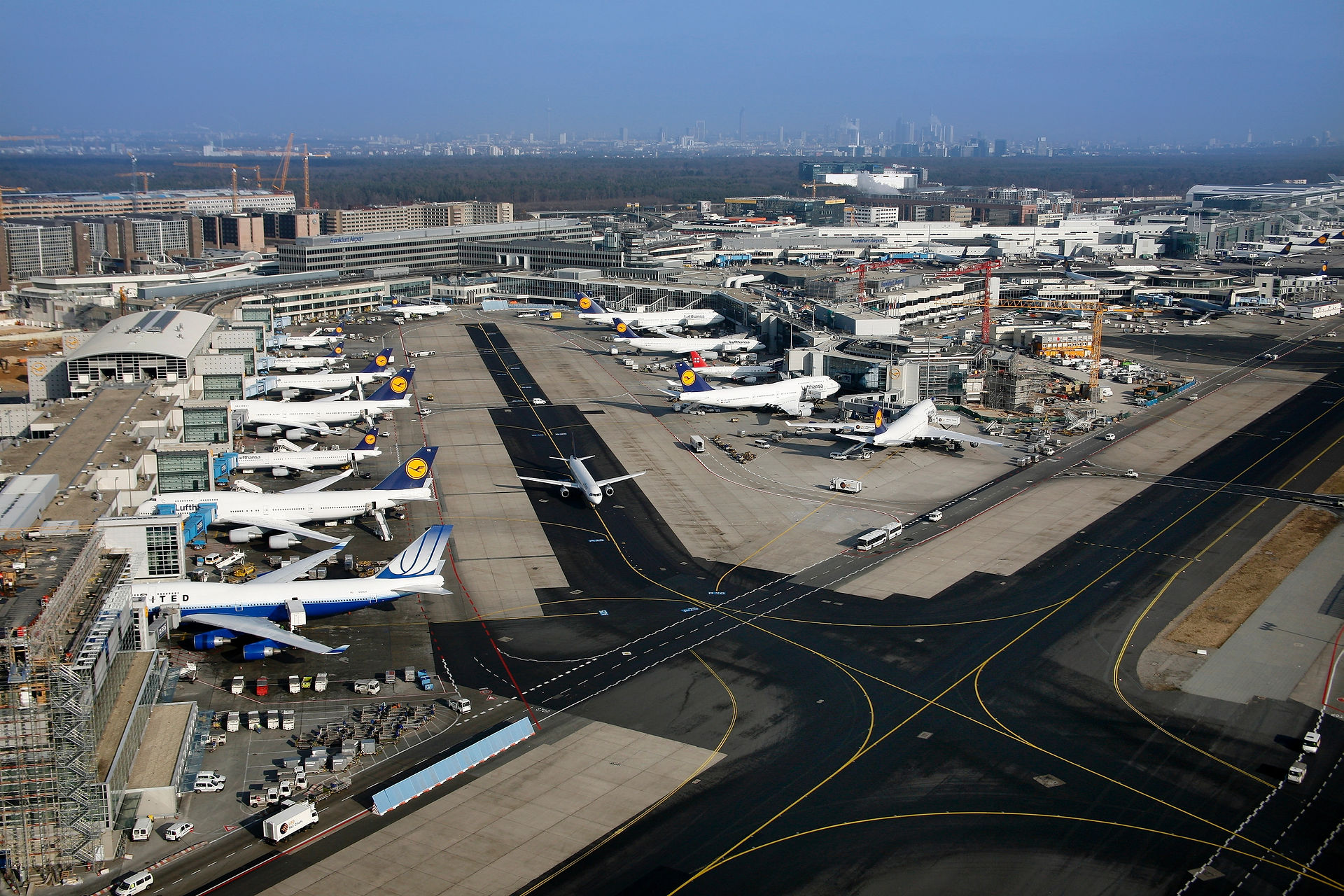

Contrac Airport Systems – Our Approach
All second hand and used airport buses are treated in 3 different, but integrated phases. In the inspection phase the used airport buses are completely dismantled and a professional team defines for each second hand airport bus the individual reworking program. Defective parts are being detected and brand new parts or ordered from the original manufacturer.
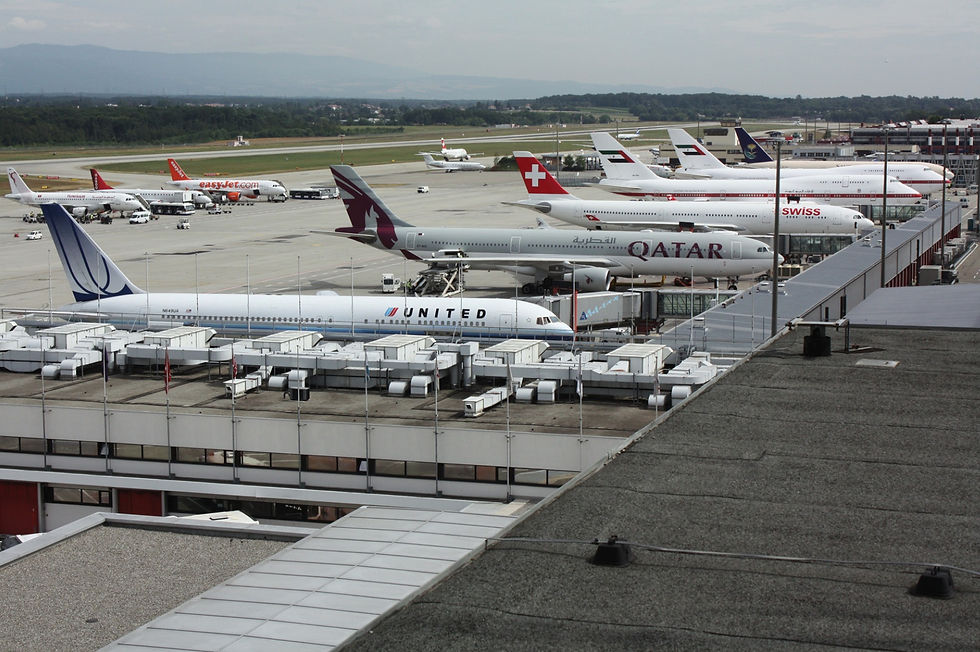
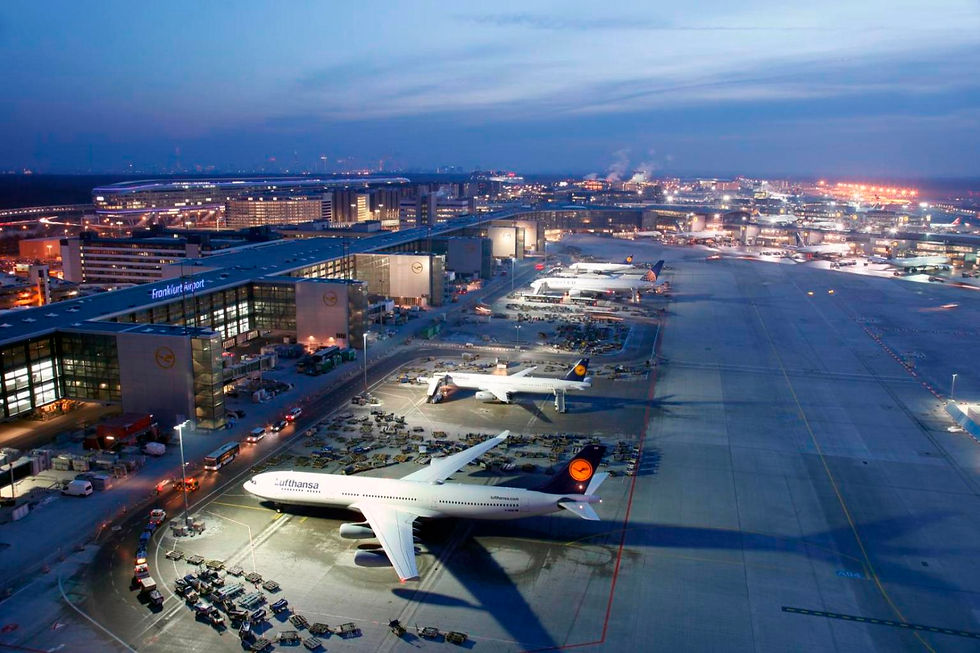


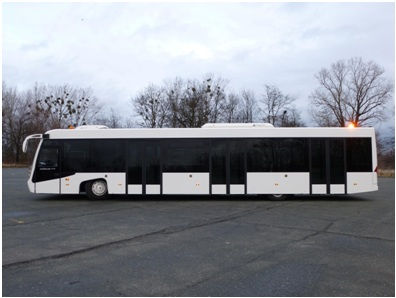

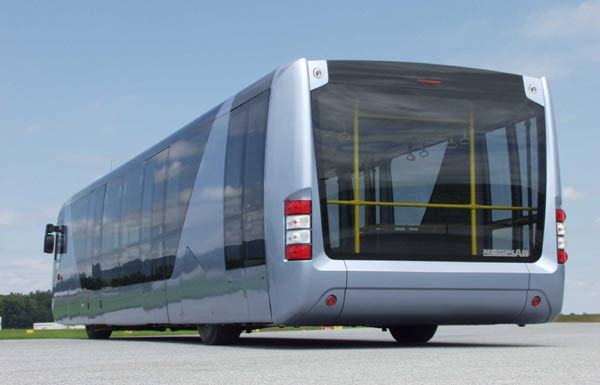

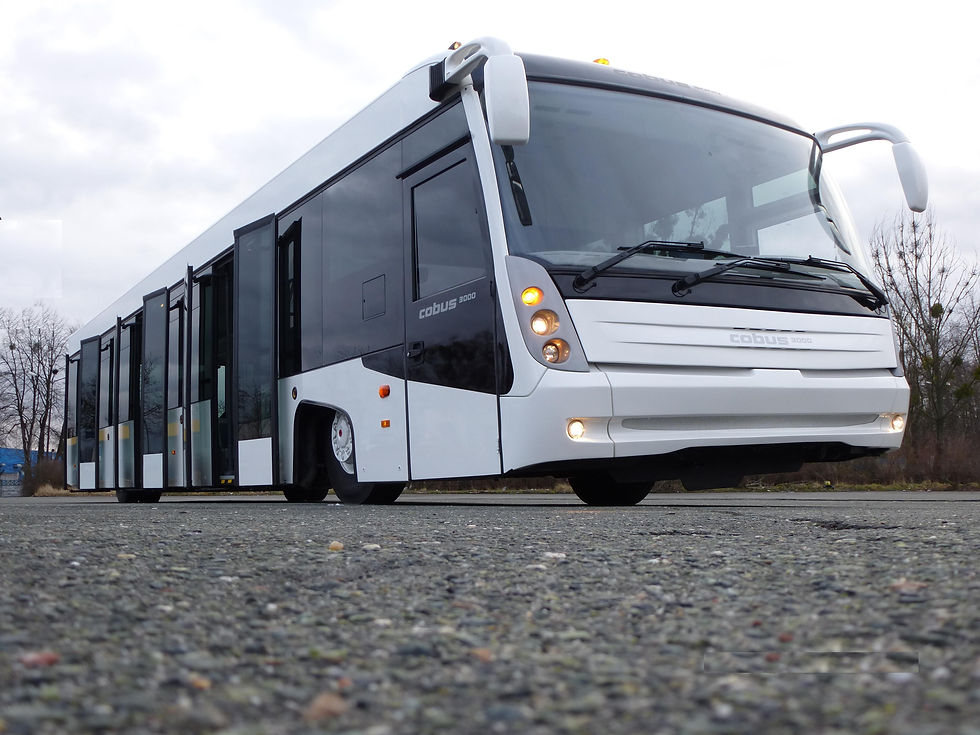
The second phase of our effort involves the re-manufacturing phase. In the production phase, emphasis is placed on having work performed by trained, skilled workers under the close supervision of experienced supervisors to ensure quality level “as good as new”. Contrac Airport Systems has an extensive workforce capable of performing all phases of re-manufacturing Airport Passenger Buses reloaded. In addition, we have skilled supervisors who have been trained and are experienced in bus rebuilding for over 20 years.
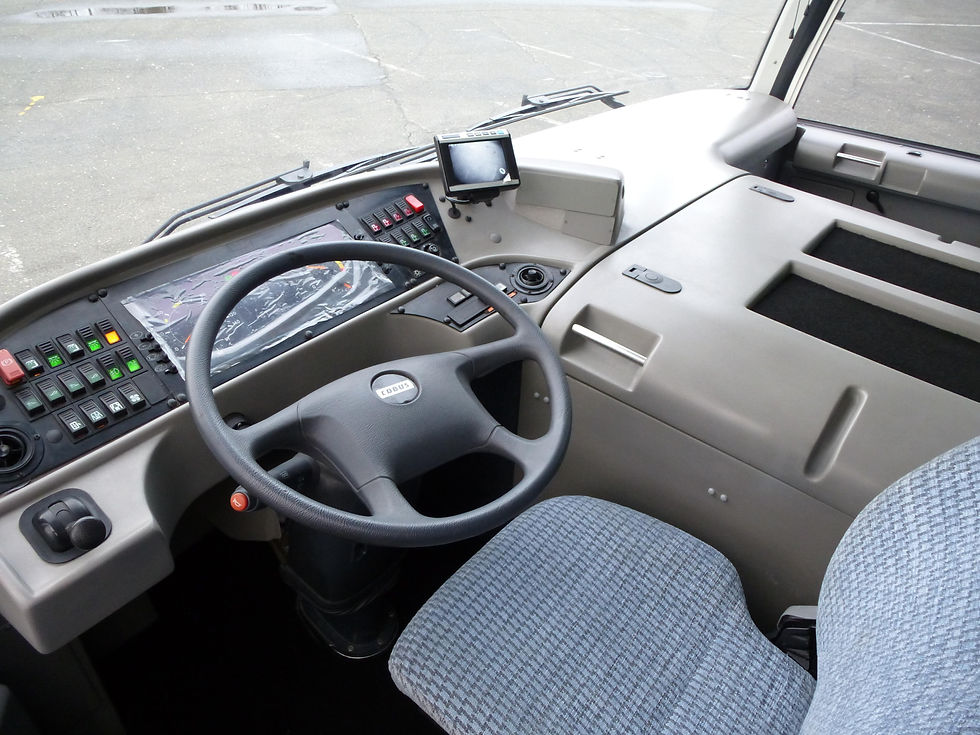
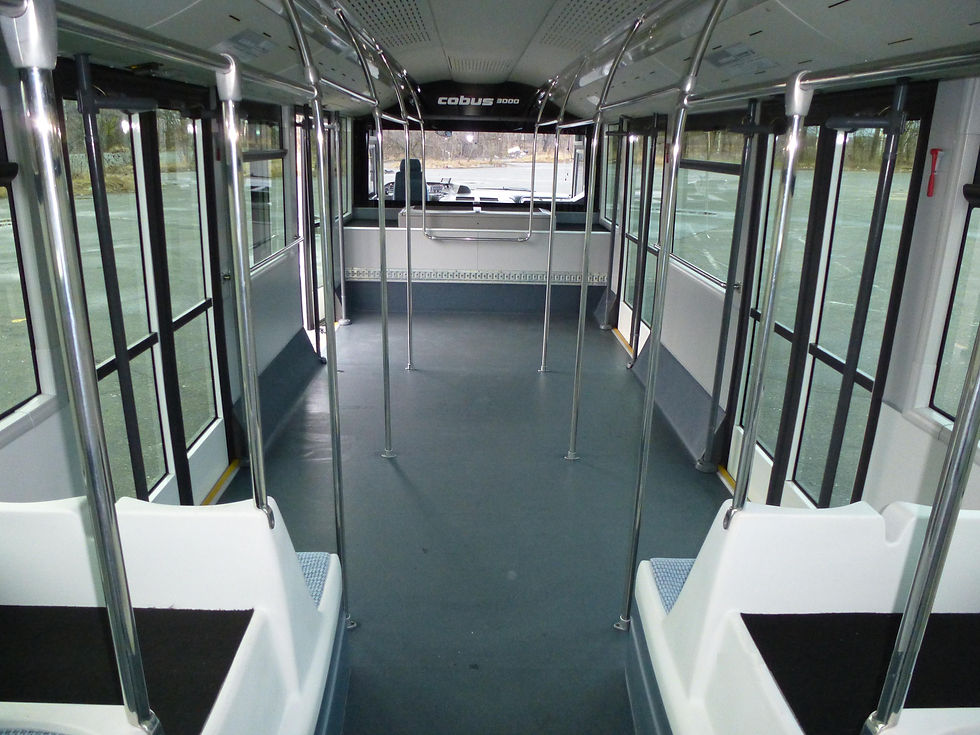
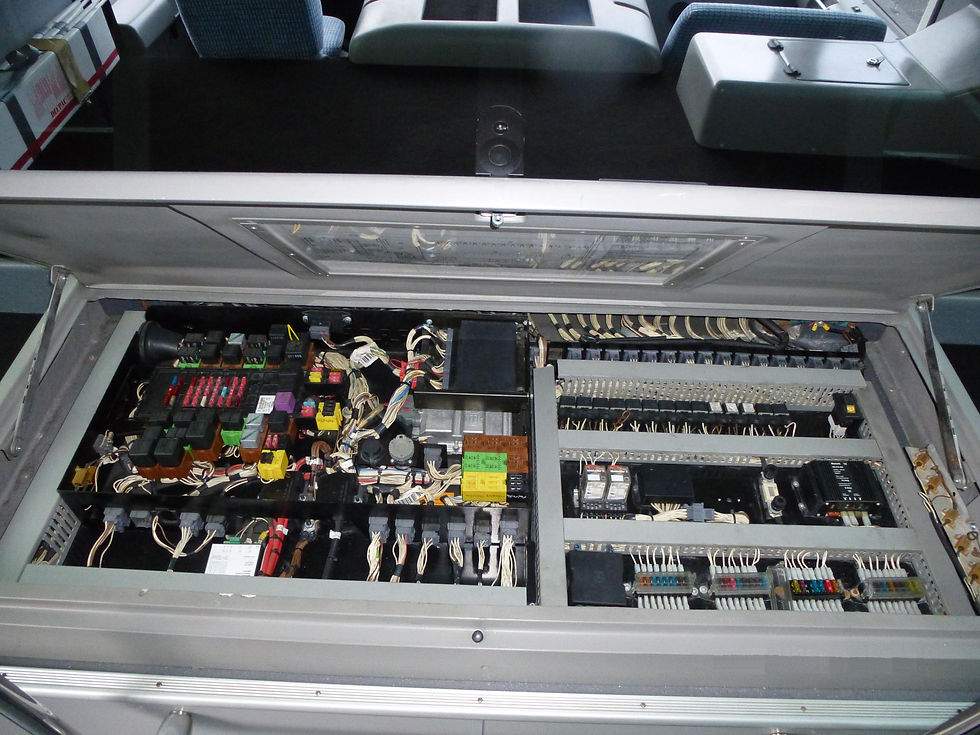

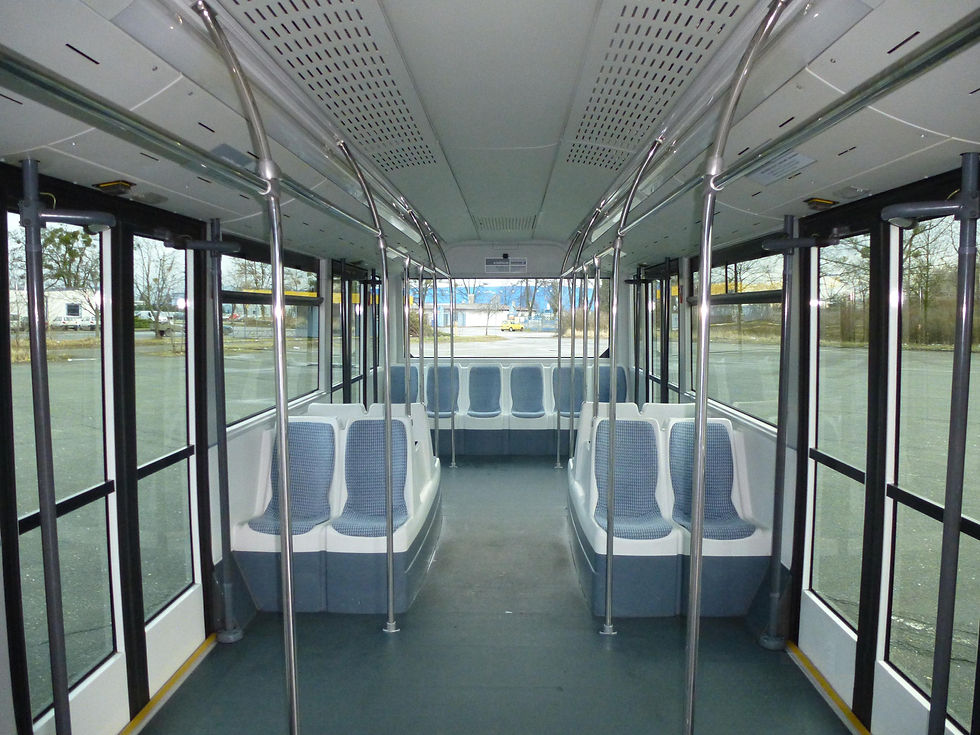

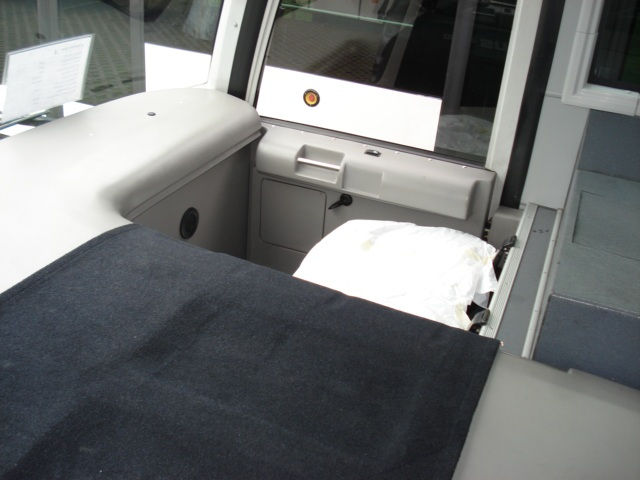
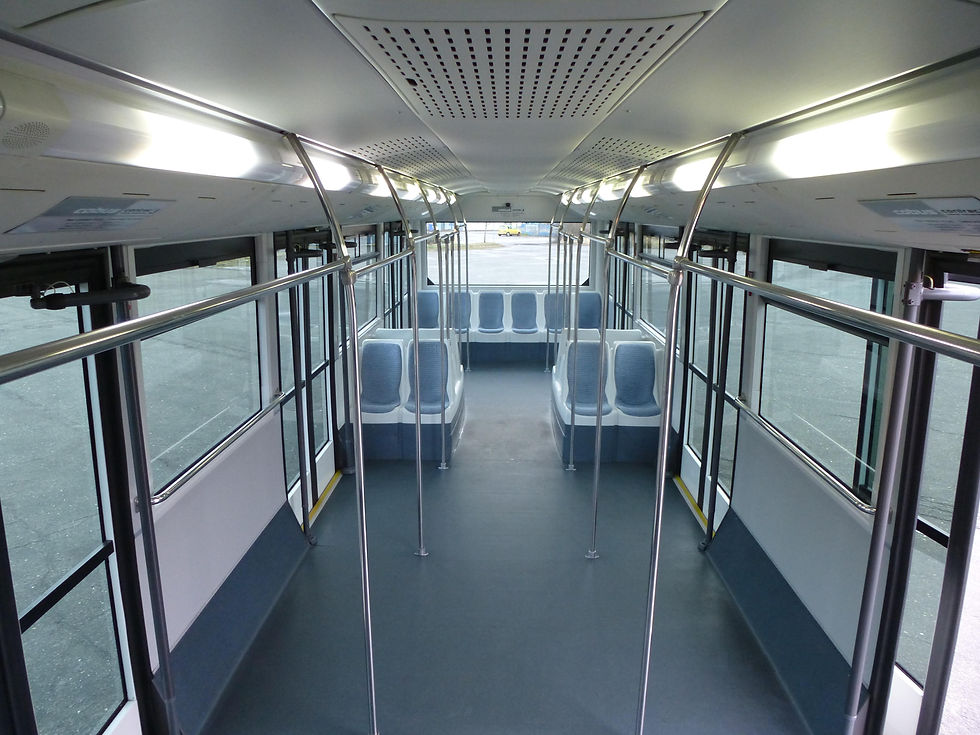
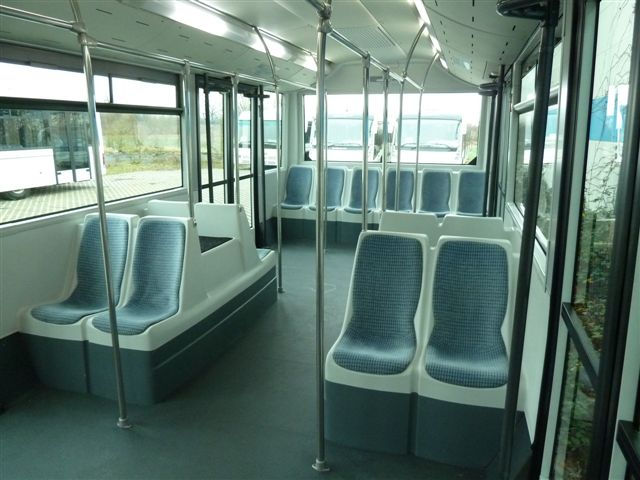
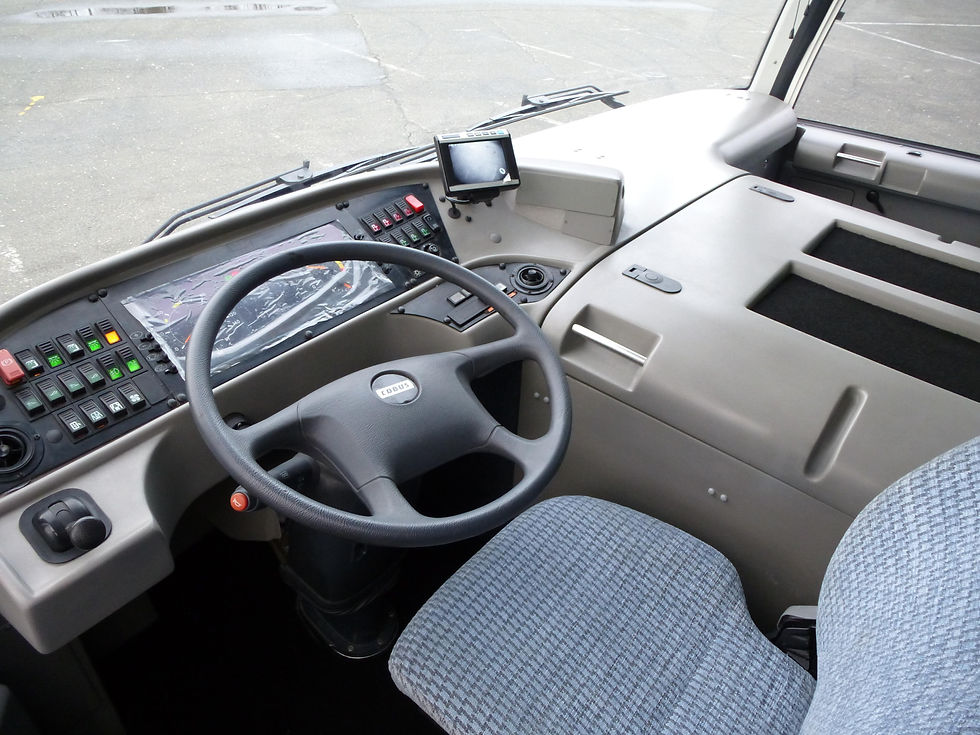
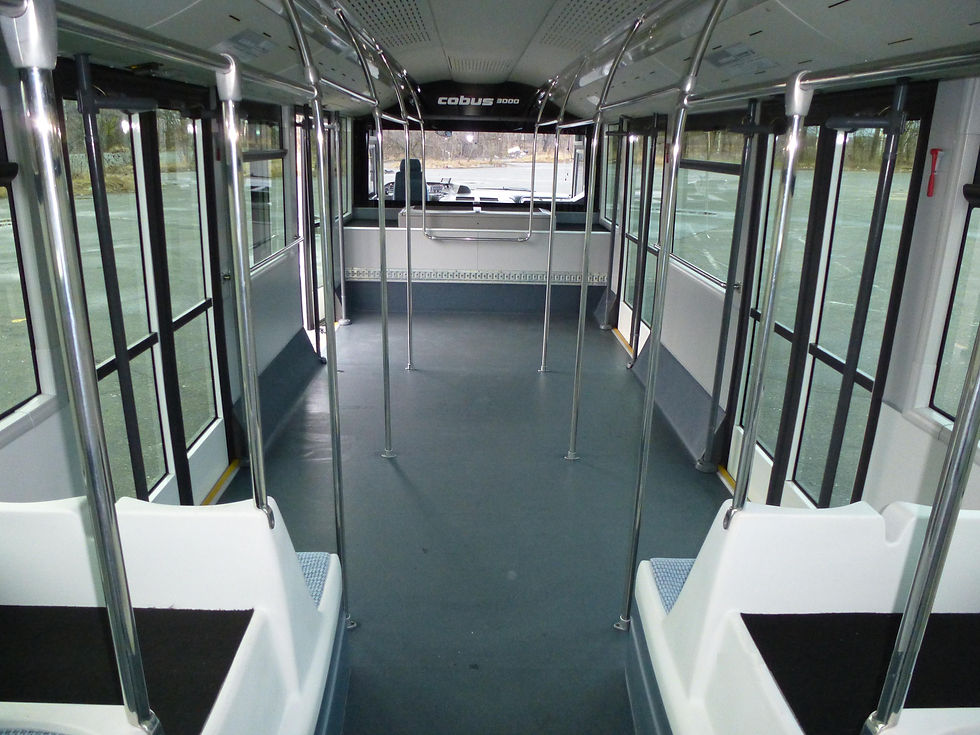
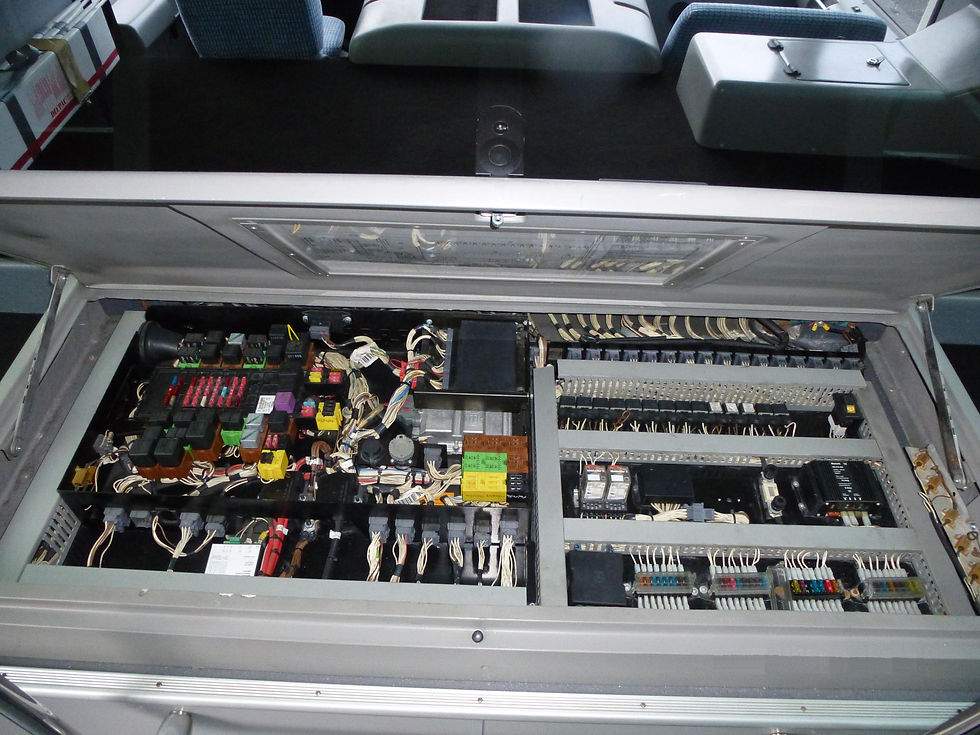

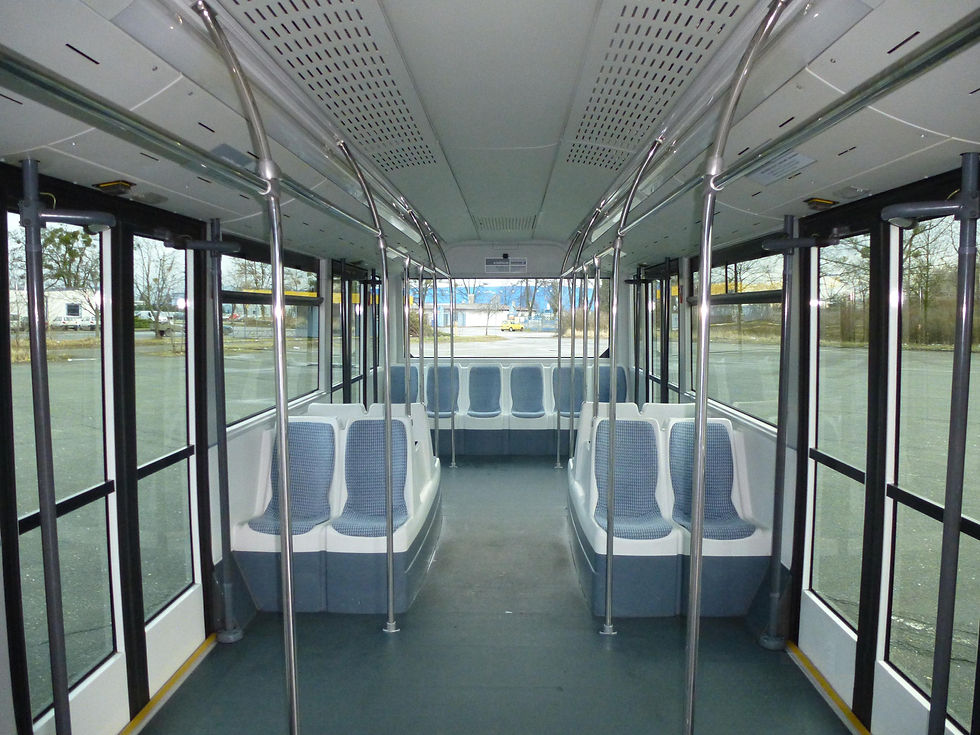

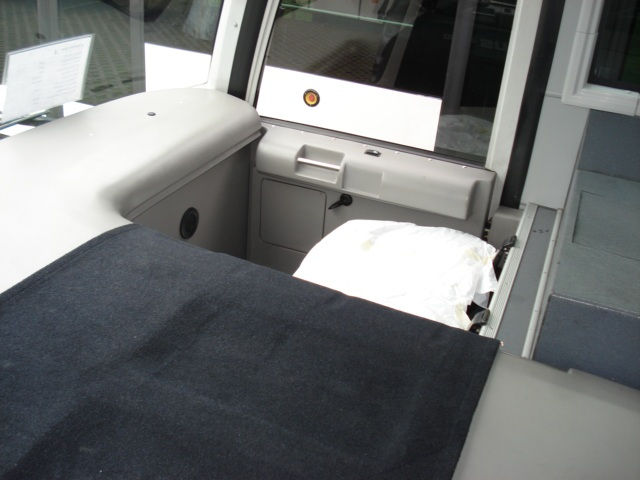
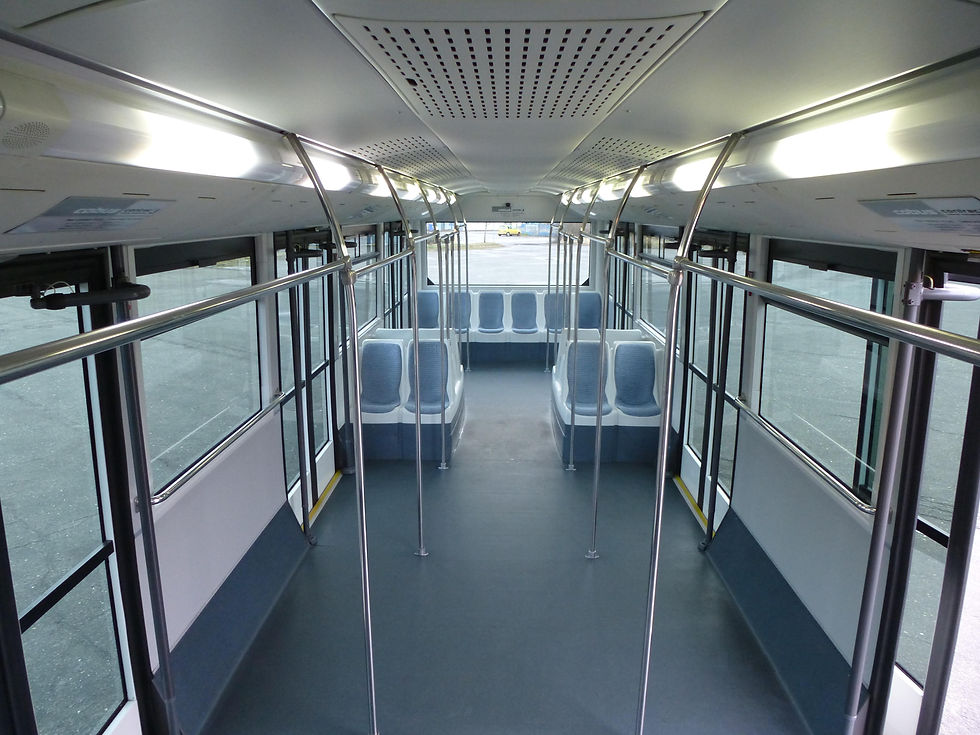
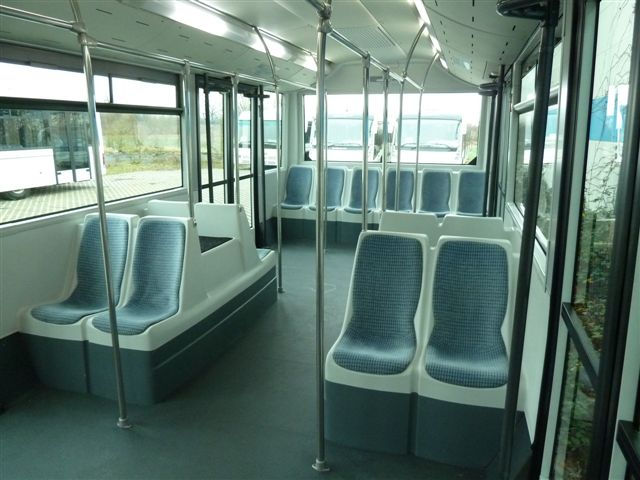
The third phase closely integrated with production is the inspection or quality control phase. Contrac Airport Systems has a full-time quality control inspection program that allows for constant scrutinizing of all work performed at each phase of the rebuilding program. Quality control personnel act independently of production personnel and report only to top management so that production schedules are never accomplished at the expense of quality. Having passed this phase, these buses can not be recognized any more as second hand or used airport buses. The buses reloaded are really as good as new.


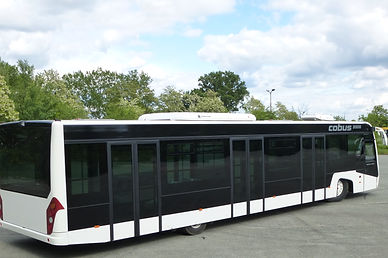
Each phase of production is carefully supervised and scheduled to ensure that the various elements of the work are completed in a timely fashion using efficient methods developed by Contrac Airport Systems. Each phase is monitored under a financial control system to guarantee the most attractive prices for remanufactured Airport Passenger Buses in a quality level “as good as new”.